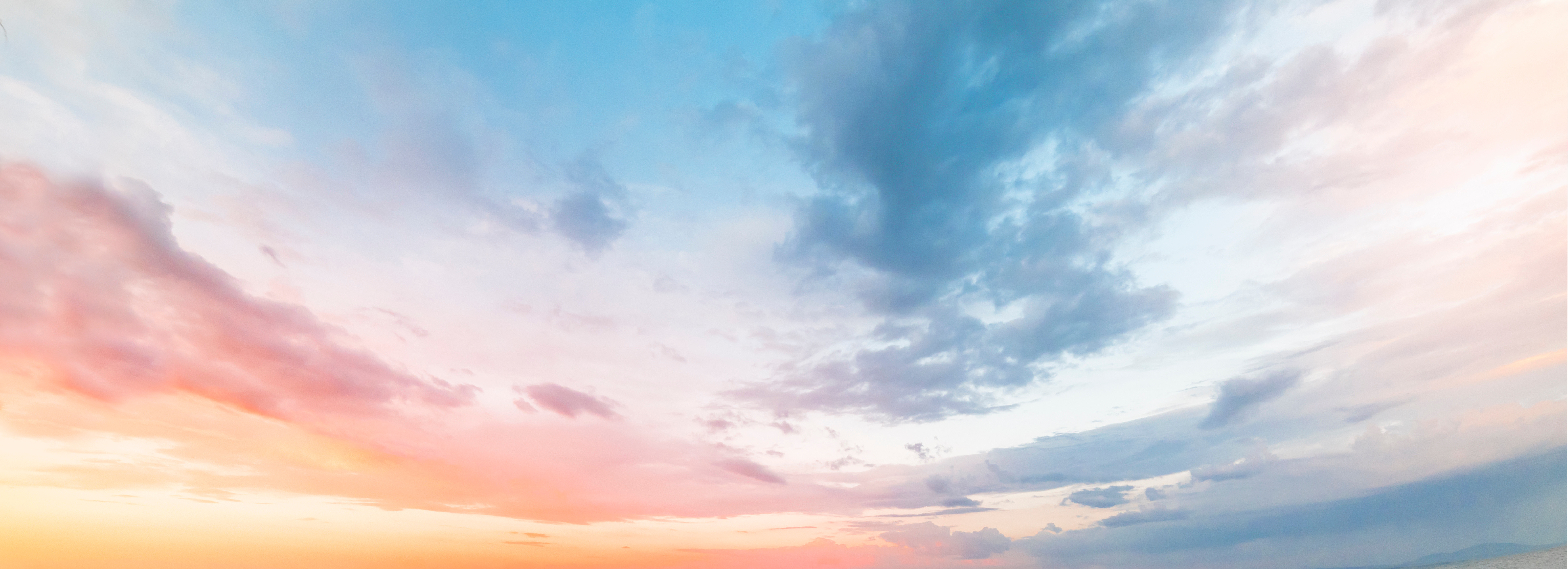
With global deployment now exceeding five million, electric vehicles continue to hold the promise of clean(er) air in our cities, yet there remains a fundamental barrier to their competitiveness: it takes over ten times longer to charge an electric vehicle than to refill a gas tank. This may soon change; researchers at Penn State University have developed an electric vehicle battery that charges in just ten minutes.
According to the team, “adding a 200-mile range in 10 min, so-called ‘extreme fast charging’, is the key to mainstream adoption of battery electric vehicles”. In fact, this is the current goal set by the US Department of Energy. Although many adopters of electric vehicles circumvent the problem by charging at home, often overnight, this does little to address the issue of range-anxiety. Defined as ‘the fear that a vehicle has insufficient range to reach its destination’, range-anxiety is prevalent among long-distance drivers. Even with an enhanced network of charging stations, fifty-minute charging times would remain extremely unattractive. Evidently, there is a need for both an increased number of charging stations and greatly improved charging speeds – only then will the electric vehicle be able to truly emulate the everyday conveniences of conventional transport.
Due to prolonged cycle life and high energy density, lithium-ion batteries are fundamental in the advancement of electric vehicle technology. However, to achieve ‘extreme fast charging’, such a battery would need to charge at a rate of 400kW, which is generally rejected due to the increased formation of anodic lithium deposits. This is commonly referred to as lithium plating, a problematic process that leads to battery degradation and reduction of charge capacity, i.e., not good for range-anxiety!
The physiochemical parameters relevant to lithium plating exhibit strong temperature dependence and plating only occurs at a significant rate when batteries are rapidly charged at temperatures below 60°C. At higher temperatures, the ion kinetics are high enough to effectively eliminate plating. Therefore, charging the batteries at a temperature above this threshold may appear to be an obvious solution. However, high temperature conditions can be equally as disastrous for a battery and would drastically shorten battery life; operating temperatures as extreme as 60°C are considered absurd.
The proposed solution is somewhat of a compromise: asymmetric temperature charging and discharging. In other words, to rapidly heat the batteries above the plating threshold, charge the battery (within ten minutes) and then rapidly cool the battery down to a non-degrading temperature for discharge (or storage). Using this method, both plating and heat degradation should theoretically be avoided.
To test this, the researchers compared the performance of industrially available batteries having undergone ‘extreme fast charging’ at temperatures ranging between 20°C and 60°C, followed by rapid cooling. To achieve the elevated temperatures, ultra-thin layers of nickel foil were inserted between the battery electrode layers, which when supplied with high current generated a heating rate of 0.8°C/s. The findings suggest that ten minutes of ‘extreme fast charging’ at room temperature can be maintained for only 60 cycles, but at 60°C the outcome is remarkably different: a battery is able to maintain 91.7% capacity after 2,500 cycles, far in excess of the US Department of Energy target. “The remarkable boost of cycle life with the increasing charge temperature […], which is contrary to the conventional wisdom, suggests that the benefits of mitigated Li plating at the elevated temperature far outweigh the negative impacts […]”.
The electric vehicle industry still faces many hurdles; for example, the battery waste problem. Nevertheless, the eventual commercialisation of extreme fast charging batteries would be a critical development. Indeed, global trends are already leaning towards a vast network of public 400kW charging stations and these newly developed batteries are the first to be compatible.
This blog was written by Michali Demetroudi.
Simon is a Partner and Patent Attorney at Mewburn Ellis. He is highly skilled in patent drafting, prosecution, oppositions and appeals. Simon is also experienced in Freedom to Operate opinions. He is particularly interested in the invention capture process, marine engineering, and automotive engineering, especially automotive safety. He leads the firm’s sponsorship of UK electric Formula Student team, Team Bath Racing Electric.
Email: simon.parry@mewburn.com
Our IP specialists work at all stage of the IP life cycle and provide strategic advice about patent, trade mark and registered designs, as well as any IP-related disputes and legal and commercial requirements.
Our peopleWe have an easily-accessible office in central London, as well as a number of regional offices throughout the UK and an office in Munich, Germany. We’d love to hear from you, so please get in touch.
Get in touch