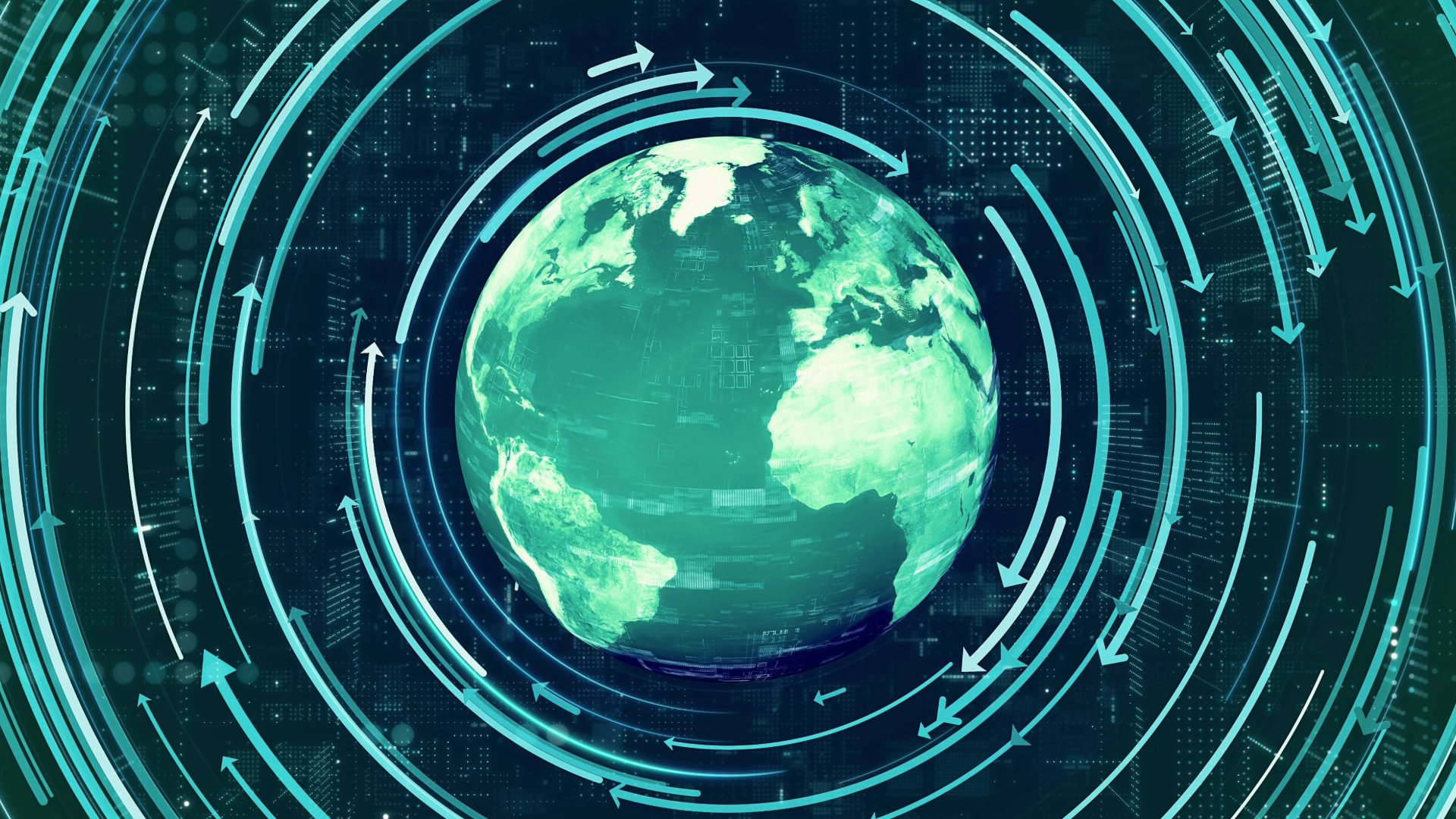
Zero-carbon transport and energy production are set to grow under the shadow of global warming and improved battery technology is going to be a key enabling technology for that growth.
Lithium ion batteries are currently thought to be the most likely contender to act as the “fuel” source of electric vehicles (EVs). They are also expected to provide the bulk of the storage capacity needed to allow renewable energy to assume centre stage in the global energy market. Research by BloombergNEF estimates that the battery industry will grow approximately 50 fold in value over the next 30 years, reaching close to $900bn by 2050.
However, limited supplies of rare and expensive elements like cobalt, manganese and nickel, which are found in the cathode materials of lithium ion batteries, are a cause for concern. Additionally, only a handful of countries generate almost all of the world’s lithium creating an unstable commercial environment for stakeholders in this area. It is estimated that the global lithium reserves are not sufficient even to replace all cars in the world with EVs, let alone provide batteries for the rest of the world’s technology too.
Simply put, current reliance on lithium ion technology, and more importantly “freshly” mined lithium, is unlikely to be able to support the imminent boom set to take place in this industry. With this mind, there are a number of areas where innovation is helping to improve the future sustainability of batteries.
Extending the life cycle of a battery is one way to improve sustainability. Many commentators are promoting a “second life” market in which batteries that have reached the end of their useful life in one application are repurposed. This could be particularly significant for EV batteries, which must operate effectively under challenging conditions; enduring both high and low operating temperatures, rarely undergoing full charge cycles, having varied power draw requirements and yet needing to maintain a long range per charge cycle.
The good news is once an EV battery can no longer meet its specific operation requirements, it may well still be able to operate in other applications. According to a recent report from Energsoft, many EV batteries are retired with up to 80% of their maximum storage capability remaining and as such they can still be implemented effectively in static utility storage facilities, where charging and discharging of the electrochemical cell is less demanding.
The Tesla project in Southern Australia for example has shown that utility storage facilities can have a huge impact on power grid stability. Services like this will be essential to mitigate against the ebb and flow of power supply from many renewable sources such as wind and solar energy. Energsoft estimate that demand for utility scale lithium battery storage will grow from ~7 GWh/y (gigawatt-hours per year) in 2020 to ~183 GWh/y within 10 years. Second life batteries are expected to be significantly cheaper than new batteries, and so demand for them is likely to be high.
That said, one of the biggest issues facing the second life industry is the reconditioning of batteries which come from various suppliers in different shapes, sizes and using different battery modalities (e.g. different electrolytes or cathodes etc.). There is currently no standardisation for batteries in EVs and this presents a challenge in efficiently incorporating batteries from different sources into the same second life solutions.
If pressure mounts for a second life market, we may find that original equipment manufacturers are incentivised to reach agreements, possibly involving IP cross-licensing, to work towards a generally applicable platform technology resulting in more certainty for second life applications.
Beyond using the same batteries for longer, by far the most obvious way to improve sustainability is to ensure that a greater proportion of the raw materials in end-of-life batteries is recycled.
Recycling of lead-acid and nickel-cadmium batteries is typically very effective, up to 99% of the battery material can be captured for re-use with current techniques. However, owing in part to the lower toxicity of the components, lithium ion batteries are recycled far less often. As a sustainability gap is becoming more apparent for lithium batteries, a shift towards a circular economy is emerging where recycled materials from lithium ion batteries are fed back into production.
The most generous reports suggest that currently 50% of Li-ion batteries reaching the end of their life are recycled. Of these recycled batteries the recovery of the essential materials is relatively low; this 50% figure does not give the full picture of what can actually be re-used in the subsequent manufacture of new batteries. In particular, the purity of recovered lithium is often too low to be suitable.
Currently, the majority of battery recycling takes place in Asia where firms are able to make a greater profit; levels of recycling in Europe are significantly lower. Some of the barriers to a higher level of recycling in Europe include difficulty in collecting and transporting the batteries and the cost of performing recycling compared with the more established Asian firms.
Despite this, a partnership announced earlier this year, between Finnish state-owned power company Fortum and another Finnish chemical side-stream processing company, Crisolteq, has seen the development of a recycling process for EV batteries in Europe which is capable of recovering up to 80% of the raw materials involved. Fortum collect, make safe for recycling and dismantle the batteries, separating out the polymers, aluminium and copper which get sent to their own recycling streams. The remaining “black mass”, which contains the precious metals and lithium from the battery, is sent on to Crisolteq who have developed an industrial scale low-CO2 hydrometallurgical process for the recovery of the metal ions from the solution.
None of Crisolteq’s published patent applications appear to relate to this process, it may be that they are protecting their “know-how” in the area as a trade secret or indeed that they have patent applications which are not yet available for public inspection. Undoubtedly, as more entrants to the raw-material recovery market arrive, holding patents which allow the exclusion of others from using proprietary methods will be an important aspect of any commercial strategy to maintain a high market share.
Improving the processes for retrieving useful raw materials from batteries is likely to be a hot topic of research in the coming years. Increasing the efficiency and bringing down the cost of material recovery from spent batteries will be essential to ensuring wide-spread uptake of recycling. Having a high-grade end product that is suitable to go back into battery manufacture would be an added bonus.
Aside from repurposing and recycling disused lithium batteries, another way to get around future sustainability problems is to develop new types of battery which are not dependent on the same raw material supply chains.
Some promising work in this area has recently been published by researchers at Skoltech in Russia. Their rechargeable cells required no lithium or rare metals in the cathode, instead they utilised a low melting point sodium-potassium alloy as the electrolyte and organic cathodes based on aromatic polymer amines. They managed to achieve a specific energy of 593 Wh/kg, more than twice that of the highest capacity lithium cells and a specific power of nearly 100 000 W/kg, a level of power that is normally only found in supercapacitors.
A further benefit of using metal alloys as electrolytes (as opposed to pure metal-ion electrolyte) and organic cathodes, is a decrease in the likelihood of the formation of metal dendrites. This is where metal builds up in small spikes that grow from the surface of the cathode. Such dendrite formation is associated with short-circuits of the battery which can lead to fires and explosions.
All in all, advances like this could eventually lead to safer and higher performance batteries which move away from the traditionally required natural resources, circumventing the lithium and rare metal sustainability problems entirely. Needless to say, new types of battery are likely to be a rich area for intellectual property filings in the next decade and beyond.
It is of course impossible to foresee exactly what the most important issues will be in the future of the battery industry. Nonetheless, the sustainability of the leading existing batteries is a looming problem that is starting to attract a great deal of investment. Against that background, there are great opportunities for innovative companies with a strong IP position to be rewarded handsomely.
Joseph is a patent attorney working in the chemistry and materials field assisting in the drafting and prosecution of UK and European patents. He also has experience in opposition and appeal proceedings before the EPO and the management of national/regional phase entry of international patent applications.
Email: joseph.newcombe@mewburn.com
Our IP specialists work at all stage of the IP life cycle and provide strategic advice about patent, trade mark and registered designs, as well as any IP-related disputes and legal and commercial requirements.
Our peopleWe have an easily-accessible office in central London, as well as a number of regional offices throughout the UK and an office in Munich, Germany. We’d love to hear from you, so please get in touch.
Get in touch