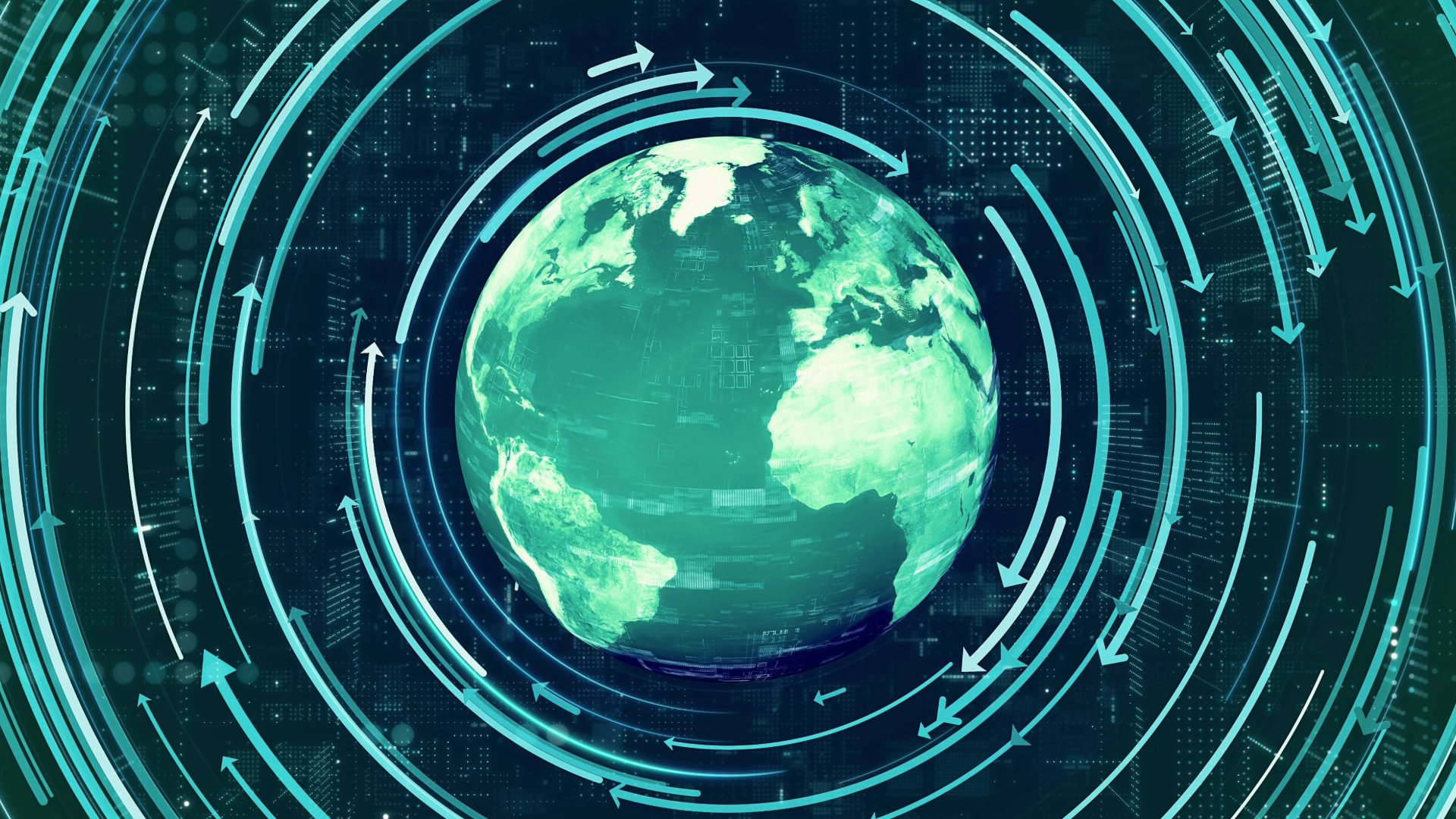
As we move towards a circular economy, there is a huge incentive for chemists to find innovative ways of handling plastics composite waste, as Thomas Lonsdale and Paul Dunne explain.
When it comes to plastics packaging, consumers and manufacturers expect big results from minimal material. Generally, packaging must be cheap, lightweight, aesthetically pleasing, and easy to handle, while providing a robust barrier to keep what is outside out and what is inside in.
It is often asking too much of a single material to meet all these requirements. In such instances, manufacturers turn to combinations of different materials to form their packaging. Such composite packaging materials find use in a wide variety of everyday items, from toothpaste tubes to tablet blisters, teabags to coffee pods, and crisp packets to food pouches.
While this wedding of materials gives huge advantages during a product’s lifetime, it complicates the sustainable disposal of the packaging. As a result, most composite packaging ends up in landfill.
Many companies are seeking to solve this problem using specialised collection systems. For example, Splosh posts home and personal care products to consumers in composite refill pouches, and asks them to return empty pouches for reprocessing. On a larger scale, TerraCycle works with brands to collect difficult-to-recycle composite packaging, such as baby food pouches and crisp packets, via public drop-off points or the post.
However, to function at scale, recycling should ideally work via home collection, instead of relying on consumers going out of their way, given the time and potential carbon footprint considerations. Unfortunately, this is currently only possible in exceptional circumstances, such as for beverage cartons in the UK. The prevalence and standardised form of this particular composite have led to a home recycling system adopted by more than 90 per cent of UK local authorities.
Once composite packaging is collected, it is then necessary to break it apart to recover the constituents for re-use. This is a significant technical challenge.
Taking the beverage carton as an example, packs are pulped, heated and acid-treated to separate the aluminium and polyethylene from the paper pulp. The paper pulp is used to make recycled paper, but the aluminium and PE remain laminated together, and are unsuitable for being repurposed in high-end applications.
This problem is not unique to beverage cartons. It is not easy to separate laminated plastics and foil. Recognising this problem, Saperatec has developed technology for breaking apart polymer-metal and polymer-polymer laminates using a ‘separation fluid’ microemulsion, and claims this is the first technology to be able to recover all individual materials from composite packaging. More recently, AKP has talked about a solvent-based process for separating the components of multilayer PE/PA6 packaging films.
While some are trying to adapt recycling systems to deal with existing composite packaging, others are approaching the problem from the other direction – developing packaging compatible with existing recycling systems. A common approach is to focus on developing composites that are compatible with existing HDPE recycling streams.
For example, Colgate-Palmolive has launched a recyclable all-plastics toothpaste tube. This tube is reported to be composed of an HDPE interior and exterior layers sandwiching a PET insert and EVOH barrier layer. The HDPE used in the tube is similar to HDPE used in bottles, allowing the tubes to be recycled via existing HDPE recycling streams. Colgate is patenting the packaging, but (unusually) has indicated that it intends to share the technology with competitors.
A number of companies have developed recyclable replacements for stand-up pouch materials, which are usually made from laminated layers of PET and PE. For example, Canadian company Nova Chemicals has created a drop-in recyclable replacement for current stand-up food pouch laminates. The pouch is made from layers of different grades of PE, which provide high levels of performance while remaining compatible with PE recycling streams. Similarly, Mondi has launched a recyclable all-PE BarrierPack pouch, which is already finding use for a variety of products.
Another company offering an alternative to non-recyclable mixed-polymer laminates is Skymark. This company has developed a range of multifunctional, recyclable PE/PE laminates to replace existing mixed laminates in a number of applications where barrier function is important, such as wet-wipe packaging.
While these innovative solutions are a clever way of complying with standard mechanical recycling systems, they are still limited by the efficiency of those systems. Arguably, existing mechanical recycling tends to degrade the quality of the polymer during reprocessing, resulting in downcycling, so that material is subsequently used for less demanding applica-tions. To realise a truly circular economy, the argument goes, it will be necessary to embrace alternatives, such as chemical recycling, which break polymers down into their constituent monomers to be rebuilt again. Some suggest this may even involve switching to entirely new polymer types specifically designed for chemical recycling, such as polydiketoamine.
Given the significant challenges presented by recycling, another option is instead to develop materials that break down in the natural environment. To this end, there is a drive towards new disposable drinks cups where the typical PE lining layer is replaced with biodegradable PLA.
In a more high-tech implementation, Lavazza recently announced its development and adoption of compostable Eco Caps coffee capsules. Lavazza’s burgeoning portfolio of patents on the technology give interesting insights into the design challenges that these biodegradable coffee pods must overcome.
Finding a place for composite packaging in a circular economy is no easy matter, so it is great to see brands across the spectrum confronting the problem. Significant challenges remain, but with increasing focus on this issue, it is hoped that investment and innovation will reap rewards for industry and society as a whole.
This article was originally published in the digital edition of Plastics in Packaging, Issue 228, October 2020. Access the original article.
Thomas Lonsdale has previously discussed plastics composite waste, and the associated challenges and areas of development, in his blog "Compostable packaging – let’s break it down".
We explore the EPO report "Patents for tomorrow's plastics" in Intellectual Property Magazine.
This article was co-authored by Thomas Lonsdale and Paul Dunne.
Thomas is a trainee patent attorney with experience in drafting and prosecution of patent applications for a range of European and international clients in the fields of chemistry, biochemistry, pharmaceuticals and materials. He has also worked on FTOs and attended proceedings before the EPO. Thomas holds a Masters (MChem) and doctorate (DPhil) from the University of Oxford in which he specialised in biocatalysis.
Paul is a Partner and Patent Attorney at Mewburn Ellis. His work is spread broadly across patent preparation, prosecution, and opposition work. Paul regularly handles opposition and appeal hearings at the EPO, where he has an excellent track record of obtaining successful outcomes for clients. He handles the coordination of third party observations against 3rd party patent applications in both Europe and the US. Paul also has particular experience, and a personal and professional interest, in the field of “green” polymer materials.
Email: paul.dunne@mewburn.com
Our IP specialists work at all stage of the IP life cycle and provide strategic advice about patent, trade mark and registered designs, as well as any IP-related disputes and legal and commercial requirements.
Our peopleWe have an easily-accessible office in central London, as well as a number of regional offices throughout the UK and an office in Munich, Germany. We’d love to hear from you, so please get in touch.
Get in touch