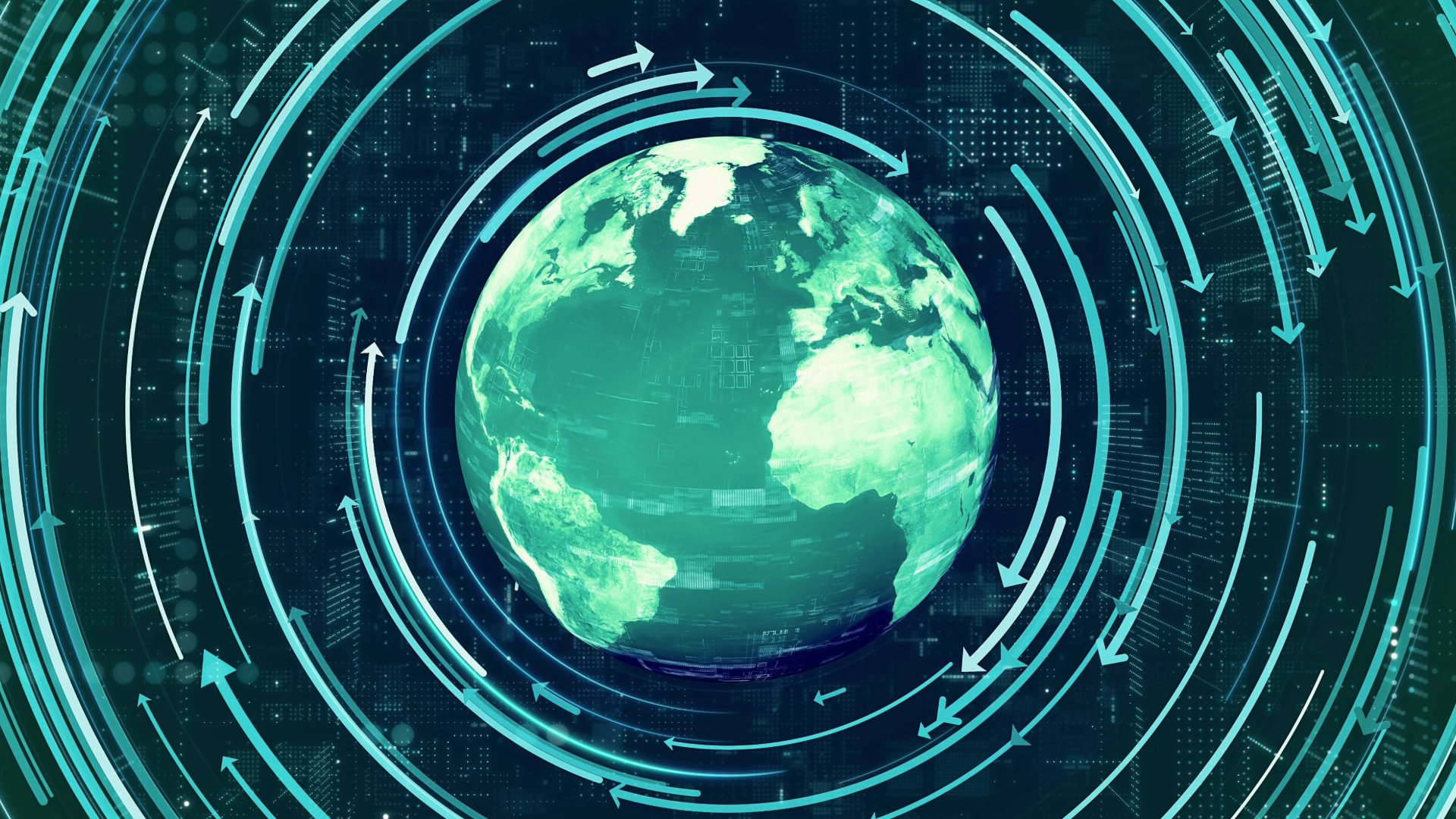
One consequence of the COVID-19 pandemic has been the significant reduction in carbon emissions in 2020. A major contributor to that reduction has been the aviation industry, with an estimated 60% reduction in CO2 emissions when compared to 2019.
Of course, that reduction is likely to be temporary, and once air travel begins to return to pre-COVID levels, the emissions will follow suit. Prior to the pandemic, the contribution to CO2 emissions from aviation matched the total emissions of the 129 lowest emitting countries combined (ranking just behind Canada in total emissions), which accounted for approximately 2% of all human-induced global emissions. This contribution is why there are now calls for the aviation industry to focus on a “green” post-COVID-19 recovery.
Fortunately for the aviation industry, they’re not starting from scratch. For some time now, aerospace manufacturers have been working towards decarbonising of air travel. Below we discuss some of the technologies these companies are exploring to reduce carbon emissions.
The adoption of electric road vehicles has seen steady growth over the last few years. A big part of that is the lack of any emissions from such vehicles, at least at the point of use (see our blog How environmentally friendly are electric vehicles?). For the same reason, aerospace companies are looking at moving from turbine engines (that make use of petroleum-based fuels) to electric motors that rely on batteries as a power source.
This, however, is a far more difficult transition than that for road vehicles. For obvious reasons, weight has a far larger impact on aircraft efficiency than road vehicle efficiency, and consequently has a significant bearing on the economics of air travel (fuel accounts for approximately 40% of aircraft weight in long-haul flights). In fact, aircraft weight is so important that in 2009 one airline asked passengers to use the toilet before boarding in order to cut down on fuel consumption.
Thus as far as aviation is concerned, an issue with batteries is that they are heavy – approximately 40 kg of the most advanced lithium-ion batteries available would provide the same power as 1 kg of aircraft fuel. This, as noted above, has an impact on the economics of electric flight, but the bigger problem is that a long-haul commercial passenger plane powered by current battery technology would simply be too heavy to leave the ground. To compound this, unlike fuel, the consumption of which reduces the weight of an aircraft during flight, batteries do not lose weight as they discharge. So, while electrification is certainly a goal of the aerospace industry, achieving that goal is likely some way off.
One way of getting to full electrification sooner is to find efficiency improvements elsewhere that reduce the power requirements of an aircraft (allowing smaller, lighter batteries). An approach being investigated is boundary layer ingestion.
In flight, a layer of slow flowing air (the boundary layer) develops around the body of an aircraft, which results in increased drag on the aircraft (and, in turn, higher fuel consumption). In commercial passenger planes the turbine engines are typically spaced below the wings, such that there is little interaction between the engines and the boundary layer. Boundary-layer ingestion is the idea of positioning the engines close to the body and at the rear of the aircraft so that they ingest some of this slow flowing air (as in this concept from NASA). The ingested air is accelerated and discharged by the engines, which has the effect of reducing the drag on the aircraft. It is estimated that this technology has the potential to reduce power consumption by 20%.
For the most part, the overall form of the commercial passenger plane (sometimes referred to as “tube and wing”) has not changed in the last 90 years. The blended wing body concept seeks to bring an end to that.
A blended wing body (as seen in this Airbus concept aircraft) involves shaping the outer skin of the aircraft so that there is no clear dividing line between the wings and the body, resulting in an aircraft that looks like a giant boomerang (although certainly not intended to fly like a boomerang). A principal advantage of this shape is that it has a smaller “wetted area” (the surface area of the aircraft in contact with airflow) than a tube and wing shape. This decreases drag and increases efficiency.
Nevertheless, there are a number of issues faced in implementing this concept. For example, a blended wing body is unlikely to be compatible with existing infrastructure and equipment (such as passenger boarding bridges used at airport terminals). There is also the issue of pressurising the interior of such an aircraft; the tubular shape of current fuselages is particularly efficient at withstanding internal pressures experienced during flight, whereas blended wing bodies may have to carry additional weight in order to be strong enough to withstand these pressures.
Hydrogen fuel, which does not produce any carbon emissions when burnt, presents an alternative to battery power. Unlike batteries, hydrogen has a greater energy density per unit mass than jet fuel, meaning that a kilogram of hydrogen will provide more energy (three times more) than a kilogram of jet fuel. The hydrogen can power fuel cells, which may produce electricity for electric motors, or can power turbine engines modified to operate with hydrogen fuel.
So why are hydrogen-powered passenger planes not yet a reality? Although hydrogen has a higher energy density per unit mass than jet fuel, it also has a lower energy density per unit volume. This means that it takes far more space to store hydrogen (for the same amount of energy), requiring a larger aircraft and more associated drag (especially for long haul flights). Like the blended wing body concept, there are also infrastructure issues: firstly, having the capability to store hydrogen at airports and, secondly, being able to produce hydrogen fuel in a carbon-friendly manner. As it stands, most hydrogen is produced using fossil fuels, so while use of the fuel does not create emissions, its production does.
This undermines hydrogen as a solution to the problem of aircraft emissions. However, in principle hydrogen can be produced using renewable energy sources rather than fossil fuels and, given solar power can now be considered cheaper than coal and gas, there are reasons to believe hydrogen can be produced in an environmentally friendly manner in the future.
Where to next? In 2016 the airline industry agreed, via the CORSIA scheme, to offset growth in CO2 emissions (from international travel) above 2020 levels. The technologies discussed above are still at an early stage, and are likely many years (or decades) from deployment, so will not help achieve that goal in the immediate future.
Fortunately, there are a number of less radical improvements that are being implemented now (or that will be in the near future) which could reduce carbon emissions. These include, for example, sustainable aviation fuels, more efficient turbine engines (for example, Rolls-Royce’s UltraFan®), and better air traffic control systems.
Further progress will, however, rely on continued investment in innovation. While the pandemic has reduced aviation industry carbon emissions, it has also had a negative economic impact on the finances of the aviation industry. If the result of that is reduced investment in innovation, then any environmental benefits resulting from the pandemic may be cancelled out in the longer term. Fortunately, the industry seems to be maintaining its focus on decarbonisation – in June this year, for example, Rolls-Royce set a goal of net zero carbon by 2050, while in September, Airbus released its three zero-emission commercial aircraft concepts, which it aims to bring into service by 2035.
Ben is a Partner and Patent Attorney at Mewburn Ellis. Ben is experienced in patent drafting, prosecution and Freedom to Operate within the mechanical engineering, medical device and consumer products sectors. He also deals with filing and infringement issues relating to registered and unregistered designs.
Email: ben.boyd@mewburn.com
Our IP specialists work at all stage of the IP life cycle and provide strategic advice about patent, trade mark and registered designs, as well as any IP-related disputes and legal and commercial requirements.
Our peopleWe have an easily-accessible office in central London, as well as a number of regional offices throughout the UK and an office in Munich, Germany. We’d love to hear from you, so please get in touch.
Get in touch