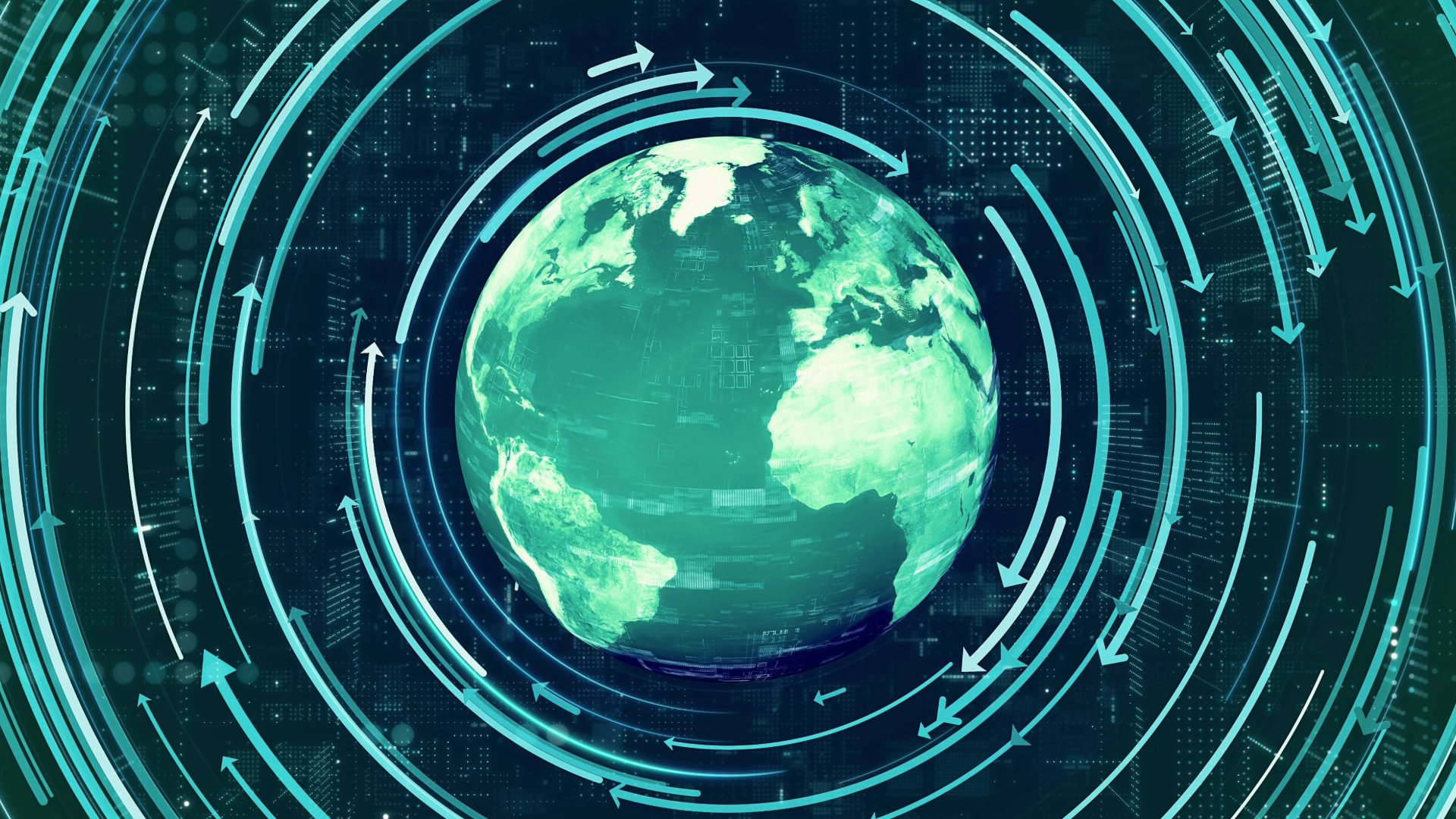
The ascent of plastic from its Bakelite beginnings to the workhorse material of the modern day has been astonishing. And despite its ubiquity, global production of the material is still growing at 3-4% every year, adding to the 8.3 billion metric tons of virgin plastics estimated to have been produced to date. With researchers at the University of California Santa Barbara estimating that, as of 2015, 79% of all the plastic ever produced had ended up in landfill or in the natural environment, the startling fact is that the majority of all this plastic persists to this day.
Increasing awareness of the environmental and economic impact of accumulating plastic waste has led to a widespread recognition that our traditional, linear ‘take, make, waste’ approach is unsustainable. There’s now a drive to develop a different approach – a so-called circular plastics economy.
Under this paradigm, plastic waste (captured through recycling or other planned collection) is processed and used as the basis for forming new materials and products, so that all plastic essentially flows around in a closed-loop system without losing material into the natural environment. The aim is to maximise the value of the plastic, minimise waste and reduce the emissions linked to its production, which are fuelling climate change.
The basic principles of the circular plastics economy are not new. For instance, the first plastic waste recycling plant was established as long ago as the 1970s. What is new is the vigour with which society as a whole, including major brand owners and policymakers, is engaging with the issue, and the widespread recognition that our efforts to date to limit the use of virgin plastics have been superficial.
Fundamental to the successful realisation of a circular plastic economy is a scaling up of global recycling efforts and capabilities. Traditionally, most recycling has taken the form of mechanical recycling, in which plastic products are processed and melted down to make new plastic resin.
However, conventional approaches can generally only tolerate uncontaminated plastics of certain types. What’s more, the processes degrade the quality of the material produced, meaning that the plastic can only be usefully regenerated a limited number of times. This leads to widespread ‘downcycling’, with plastic bottles being used to make carpets or fleece vests, for example.
Innovators such as Klaus Feichtinger and Manfred Hackl, winners of the European Patent Office’s European Inventor Award 2019, are developing new processes to improve the quality of the material produced by these mechanical recycling methods. Their patented Counter Current technology allows more types of plastic waste to be converted into high-quality pellets ready for industrial reuse as new products, with greater efficiency.
Other innovators are pursuing chemical recycling options, in which plastic polymers are broken down into their constituent monomer units to be used as the basis for forming new plastics. For example, Loop Industries has developed a method for breaking down traditional PET bottles by hydrolysis, and has already established supply agreements with Coca-Cola, Danone and Pepsi.
A team at the Lawrence Berkeley National Laboratory in California has taken an entirely different approach: not trying to make do with recycling existing materials, but instead designing an entirely new type of chemically recyclable plastic called PDK (polydiketoenamine). The inventors have shown that this polymer can be broken down into monomers in an acidic solution. Once deconstructed to its basic building blocks, the plastic can be rebuilt from scratch, without being constrained by the nature of the plastic’s former incarnation (its colour, for instance). The inventors claim that this allows for repeated recycling, without any loss of performance.
Of course, the scale of the challenge in realising a circular plastics economy is huge, and the exact path to success is not yet entirely in sight. However, what’s clear is that the development of a broad range of innovations has a key role to play in closing the loop.
We explore the EPO report "Patents for tomorrow's plastics" in Intellectual Property Magazine.
This article was originally published in the third edition of Mewburn Ellis Forward — a biannual publication that celebrates the best of innovation and exploration.
Subscribe to Mewburn Ellis Forward here.
Paul is a Partner and Patent Attorney at Mewburn Ellis. His work is spread broadly across patent preparation, prosecution, and opposition work. Paul regularly handles opposition and appeal hearings at the EPO, where he has an excellent track record of obtaining successful outcomes for clients. He handles the coordination of third party observations against 3rd party patent applications in both Europe and the US. Paul also has particular experience, and a personal and professional interest, in the field of “green” polymer materials.
Email: paul.dunne@mewburn.com
Our IP specialists work at all stage of the IP life cycle and provide strategic advice about patent, trade mark and registered designs, as well as any IP-related disputes and legal and commercial requirements.
Our peopleWe have an easily-accessible office in central London, as well as a number of regional offices throughout the UK and an office in Munich, Germany. We’d love to hear from you, so please get in touch.
Get in touch