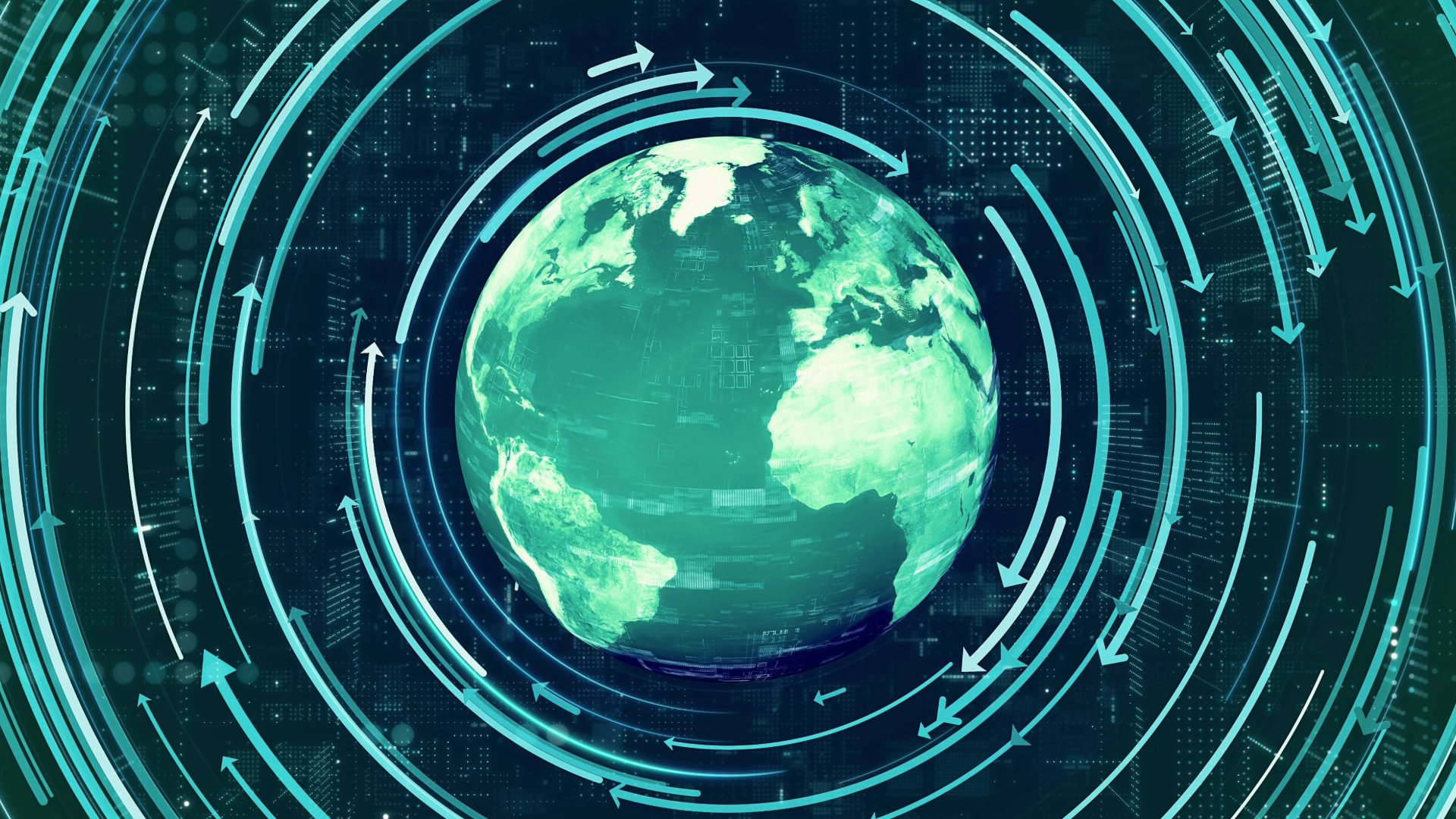
Global energy consumption has more than doubled in the last 30 years, with much of the increase coming from solar, wind and other intermittent renewable energy sources. Electrical vehicle (EV) use is also soaring; global electric car stock increased by almost 50% in the period 2018-2019, and this can be expected to continue in light of the many regulations phasing out diesel and petrol vehicles in the coming decades. To cope with this large increase in demand for electricity storage, for both sporadic output energy sources and EVs, a revolution in the way we manage battery technology is required.
Current rates of battery module production are huge. Not only does this contribute to significant demand for raw materials, many of which are sourced almost exclusively from politically unstable areas, but the rate at which new products are made outstrips our capabilities to safely reprocess and recycle spent or degraded batteries.
The EU commission announced the first update to the EU Battery Directive in more than decade to keep abreast of these changes. EV battery manufacturers will, under these changes, be required to report the recycled content of their products. It is hoped that this will incentivise meeting the 2030 EU targets for minimum recycled content of 12, 85, 4 and 4% for cobalt, lead, lithium and nickel respectively, safeguarding the supply of these largely non-Union derived materials for manufacturers.
This renewed focus on recycling and harnessing secondary raw materials provides ample opportunity for innovation.
There is no industry-wide approach to battery recycling, and there are many efficiencies that can be made at many processing stages. The form of battery modules vary hugely from product to product and there are significant health and environmental hazards to surmount: batteries may discharge during handling, noxious chemicals can be given off if components are damaged. Even the main components of batteries are often toxic, flammable and carcinogenic. Automated and semi-automated solutions or even “smart” systems as have been proposed for nuclear waste decommissioning, are a huge area for potential development towards high-throughput recycling capability.
Processes to reclaim reagent-grade starting materials from battery materials are still fraught with challenges when considering commercialisation. Substantial quantities of environmentally concerning solvents are used in metal reclamation and in the sifting necessary to remove carbon, lithium salts and polymers, in addition to high cost metallurgical processing for cobalt and nickel retrieval. Improved methods, chemical compositions and processes highlighting reclamation efficiency, specificity, energy savings and process time reduction are critical for ensuring that material supply keeps up with the demands for energy storage.
Equally, another huge area for optimisation could be the development of electrode materials directly from mixed waste streams to reduce the reliance on pure reagents. Indeed, any industry relying on raw materials derivable from battery materials are likely to benefit from this sharpening focus of the EU commission, from catalysts for water treatment to materials in other electrochemical applications like hydrogen generation for fuel cells.
Whilst recyclable content thresholds will clearly be a benefit to those industries and researchers specialising in the processing of battery materials and use of secondary raw materials, it is a part of a wider strategy of “reduce, reuse, recycle” discussed in our earlier blogs Taking charge - repurposing, recycling and reinventing batteries and How environmentally friendly are electric vehicles? Legislation concerning the sustainability of the industry will help stimulate a wider infrastructural development – opportunities may well arise in areas like systems reintegration of second-life batteries from EVs or grid storage.
National and international consortiums like ReLiB, ReCell and ReLieVe are already contributing to the burgeoning area of battery material recycling. Both the academic institutions and industrial partners hope to exploit the opportunities that directives like this bring, and as the scope of the opportunities become clearer it is expected that further areas will become ripe for exploitation. As the EU Commissioner for Environment, Oceans and Fisheries Virginijus Sinkevicius suggests, the legislation is hoped to help create a “sustainable batteries value chain”. While the raw material accessibility and reduced environmental impact are critical drivers for these new regulations, the desired stimulation of a circular economy is a chance for innovators across a broad swathe of sectors to benefit from a renewed focus on sustainability and value-adding processes for waste-streams.
This blog was originally written by Ben Baker.
|
Battery insights & IP trends - Special Report 2023This report demonstrates how innovation is blossoming in all areas of the battery ecosystem driven by both pressures and incentives; and how patents are playing a big part in protecting inventions and forming one branch of a wider commercial strategy. |
Sam is a Partner and Patent Attorney at Mewburn Ellis. He works principally on chemistry and materials science patents. Sam has extensive experience drafting new patent applications and coordinating prosecution and grant worldwide. He also regularly represents clients at EPO oppositions and appeals. Sam has a particular interest in Supplementary Protection Certificates (SPCs) and leads our SPC group.
Email: sam.bailey@mewburn.com
Our IP specialists work at all stage of the IP life cycle and provide strategic advice about patent, trade mark and registered designs, as well as any IP-related disputes and legal and commercial requirements.
Our peopleWe have an easily-accessible office in central London, as well as a number of regional offices throughout the UK and an office in Munich, Germany. We’d love to hear from you, so please get in touch.
Get in touch