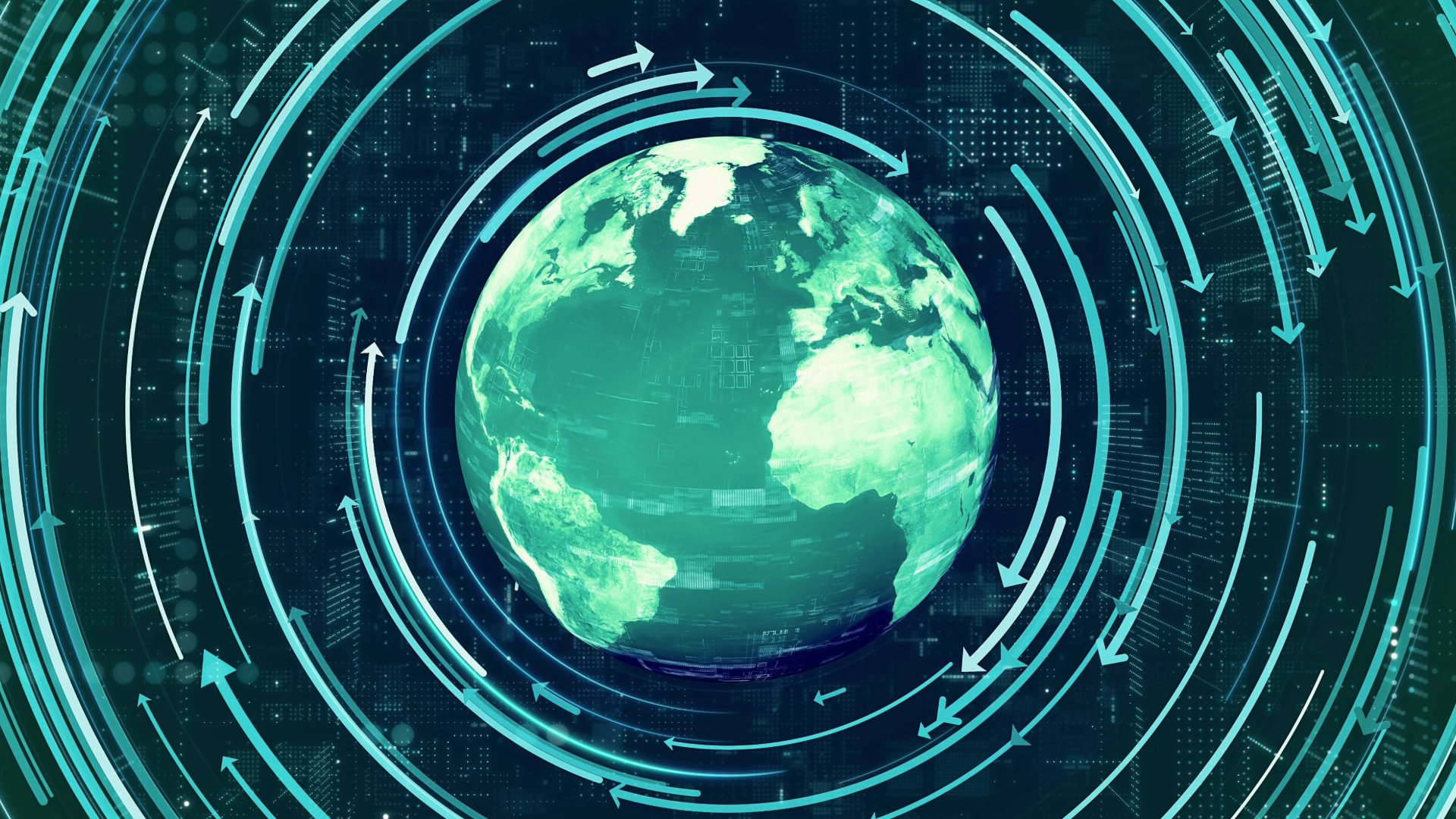
In the UK alone 35.8 million plastic bottles are used and discarded every day. And, with approximately 20,000 bottles weighing approximately one tonne, this is the equivalent in weight to approximately 149 double decker buses.
Needless to say, the relationship between human activity and single-use plastics is having a devastating impact on the environment. With global concern about the harmful impact of plastic on the environment intensifying, the proverb of the “three Rs” (reduce, reuse and recycle) has emerged as a pithy outline of the key strategies for reducing the environmental impact of our unhealthy reliance on single-use plastics.
One creative method of reuse is that of “upcycling”, in which plastic waste is re-purposed to provide a new higher quality product.
In this connection, a number of tyre manufacturers – with their sights set on providing tyres made from recycled or sustainable materials – have turned their attention to plastic waste as a source of “upcyclable” material.
At face value it’s easy to assume that tyres are a rudimentary technology, it’s just a rubber ring with treads, right?
Not quite. Underneath the outer rubber tread lies a complex laminate architecture that can be split into two main structural elements; (1) the tread and belt assembly and (2) the carcass (or casing). These elements consist of several different layers made of various materials (e.g. rubber, steel belts, textiles etc). Each layer is crucial to providing a tyre that can support the weight of the vehicle, adapt to changing road conditions and ensure the safety and comfort of passengers.
The carcass, in particular, represents the framework of the tyre. It consists of various layers that together function to contain the air within the tyre. In one such layer, polyester yarn – specifically polyethylene terephthalate (PET) – is used to provide a textile reinforcement layer that sustains the load and absorbs shock.
Virgin PET, being typically manufactured from petrochemical sources, isn’t an environmentally friendly option. Recognising this, a number of tyre manufacturers have reconsidered their options for sourcing PET yarn.
One creative solution from Continental, in collaboration with the fibre specialist and textile manufacturer OTIZ, is to upcycle PET from discarded plastic bottles into high performance PET for use in tyre carcasses.
The process developed by Continental and OTIZ avoids the chemical steps previously required for recycling PET from bottles. Instead, a mechanical process is employed in which the bottles are first mechanically shredded, then melted down and granulated, followed by solid state polymerisation and finally spinning the upcycled PET into fibers.
Using the new process, 60 recycled PET bottles can provide sufficient material for a complete set of vehicle tyres. And Continental have announced that from this year upcycled PET will completely replace conventional virgin PET in the construction of Continental tyre carcasses.
In a similar vein, Michelin in collaboration with biochemicals company Carbios S.A have also investigated upcycling PET plastic waste into technical grade PET yarn for tyre applications. The Michelin / Carbios recycling process utilises an enzyme that is capable of depolymerizing the PET plastic waste back into its constituent monomers. The resultant monomer feedstock can then be re-polymerized back into PET to provide a high grade fibre that can be used in tyres. And Michelin consider that “nearly 3 billion plastic bottles per year could be recycled into technical fibres for use in the Company’s tyres”. You can read more about Carbios' process in our blog A Taste for Waste – Plastic Recycling with Enzymes.
Upcycling plastic waste isn’t just limited to PET bottles. Efforts are also being made to repurpose other components of plastic waste for tyre manufacture.
Enter polystyrene, one of the most widely used plastics, and indeed one that we’re all familiar with as that irksome white foam accompaniment to flat pack furniture. Vast quantities of polystyrene are thrown away everyday in the form of disposable cups, food containers, and packaging etc.
The building block of polystyrene is styrene monomer. However, styrene monomer isn’t solely used to manufacture polystyrene, it is also one of the building blocks for manufacturing synthetic rubber, which is a crucial component of most vehicle tyre treads.
Consequently, waste polystyrene offers a potential feedstock of styrene monomer that is prime for upcycling into tyres.
In this connection, Michelin have joined forces with Canadian firm Pyrowave to investigate generating recycled styrene monomer from waste polystyrene using Pyrowave’s microwave-based technology. The recycled styrene monomer providing a feedstock that can be upcycled into high performance products such as synthetic rubber for tyres.
An outright ban, or at least a significant cull, of conventional single-use plastics is the desideratum. However, in view of our heavy reliance on plastic, it seems unlikely that such a drastic change will be implemented in the foreseeable future. And so, until this time, continued creative and innovative efforts are required to reduce the quantity of plastic ending up in landfill.
The upcycling of waste plastic into high quality / high performance products such as tyres represents one of these innovations.
Rebecca is a patent attorney in our chemistry team, her work includes drafting and prosecuting patent applications in the UK and Europe, for clients in the chemical sector. She is also experienced in invention capture and filing strategy. Rebecca has a MSci degree and PhD in chemistry from the University of Nottingham. The main focus of her doctorate research was to understand how the molecular structure of ionic liquids can influence their inter-ion interactions and bulk/surface properties.
Email: rebecca.blundell@mewburn.com
Our IP specialists work at all stage of the IP life cycle and provide strategic advice about patent, trade mark and registered designs, as well as any IP-related disputes and legal and commercial requirements.
Our peopleWe have an easily-accessible office in central London, as well as a number of regional offices throughout the UK and an office in Munich, Germany. We’d love to hear from you, so please get in touch.
Get in touch