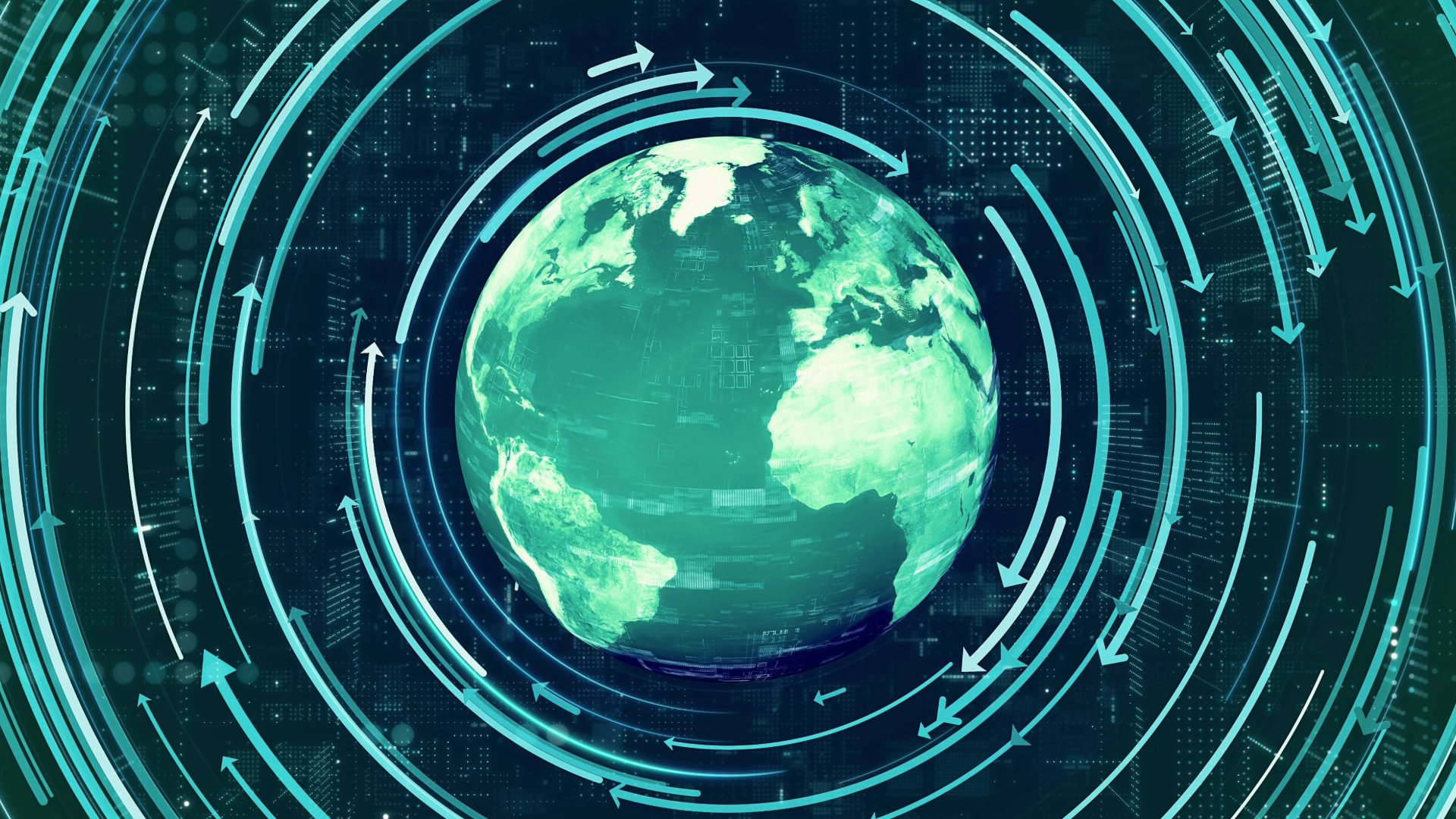
Graphene has generated a tremendous amount of excitement since it was first isolated at the University of Manchester. Quickly designated as a “wonder material”, graphene is the thinnest, strongest and most conductive material known to exist. As a result, graphene has the potential to disrupt a wide range of industries.
But if graphene is stronger than steel, more conductive than copper and has a higher electron mobility than silicon then why, for example, are we not already seeing graphene widely used in construction, conductive inks and electronics?
The reasons are well-known. Graphene has been both expensive and challenging to manufacture on a commercial scale. This has created a critical bottleneck that has limited the widespread rollout of products containing graphene.
But this is changing rapidly. The price of graphene has fallen dramatically since its discovery, as production capacity increases and as new methods for producing graphene at lower costs are developed.
Quality Matters
In any discussion about the cost of manufacturing graphene it is important to be clear about both the type and quality of graphene. Many people imagine graphene to be simply a defect-free monolayer of carbon atoms. In reality, so-called pristine graphene is only one of many varieties of “graphene”, and represents only a small minority of graphene sold commercially.
Imperfect forms of graphene are more commonly used, such as graphene nanoplatelets and reduced graphene oxide. While these do not have quite as impressive properties as those associated with the “wonder material” pristine graphene, they still provide enough of a benefit to have been widely implemented into next generation sports equipment, composites, and anticorrosion coatings, for example. Importantly, these imperfect forms of graphene can be produced at relatively low cost and on a much larger scale.
Bringing the Cost Down
While “top-down” techniques for preparing graphene have been known for some time, major advances have been made in optimising these methods, and developing new methods, particularly in the past decade.
For example, liquid-phase exfoliation has been a go-to technique for preparing graphene nanoplatelets for 15 years. Even so, the cost of producing graphene made by liquid-phase exfoliation continues to go down as methods that improve the yield of graphene and reduce the exfoliation time and temperature are discovered.
Economies of scale are another important factor. The global graphene market has grown significantly in recent years, and is set to continue at a compound annual growth rate of 43.2%1. Inevitably, as production volumes of graphene are increased to meet growing global demand, the price of graphene declines.
Indeed, leading graphene manufacturers are already exploiting these developments to such an extent that even pristine graphene is becoming increasingly viable as a commercial material. Graphenea describe pristine graphene at prices below €2 per cm2, down from €1000 per cm2 10 years ago.
Pristine graphene is most commonly manufactured by chemical vapour deposition. Unlike graphene nanoplatelets and reduced graphene oxide, chemical vapour deposition produces graphene by a “bottom-up” approach, with individual carbon atoms being deposited on a substrate to form a graphene monolayer.
This can be a slow process that is difficult to replicate on a commercial scale. One problem is that chemical vapour deposition is normally performed in a quartz tube. This limits the size of graphene sheets that can be produced, and quartz has been linked to graphene contamination.
Advancements have been made that remove the need for a quartz tube as a reaction chamber, improving both the quality and scale of production of pristine graphene grown by chemical vapour deposition. As a result of this and other developments, sheets of pristine graphene that are several square metres in size are now being made. Production of graphene sheets at this scale helps meet the growing demands of the industry.
Applied Graphene Materials have developed an innovative alternative “bottom-up” method for manufacturing graphene. An important advantage of their technique is that it is substrate-free, and so removes the laborious step of separating the graphene film from the substrate on which it is deposited. Removing this step also makes the entire process continuous, which significantly increases the volume of graphene that can be produced.
Outlook
In the past few years in particular, graphene has been making the leap from academic fairytale to global commercial reality. The industrial significance of graphene has never been in doubt; instead, it has been its cost and supply acting as barriers to its widespread use. With the cost of graphene at an all-time low and scales of production greater than ever, we might finally be seeing these barriers fall.
[Graphenea data for reference]
1 Graphene Market Size, Share & Trends Analysis Report 2021-2028, Grand View Research, Report ID: 978-1-68038-788-9.
|
David is a trainee patent attorney working in the fields of chemistry and materials. His areas of expertise include inorganic and organic synthesis, advanced inorganic materials, luminescent materials, gas storage and separation technologies, two-dimensional materials, including graphene, and synthesis and characterisation of crystalline materials.
Email: david.brooks@mewburn.com
Our IP specialists work at all stage of the IP life cycle and provide strategic advice about patent, trade mark and registered designs, as well as any IP-related disputes and legal and commercial requirements.
Our peopleWe have an easily-accessible office in central London, as well as a number of regional offices throughout the UK and an office in Munich, Germany. We’d love to hear from you, so please get in touch.
Get in touch