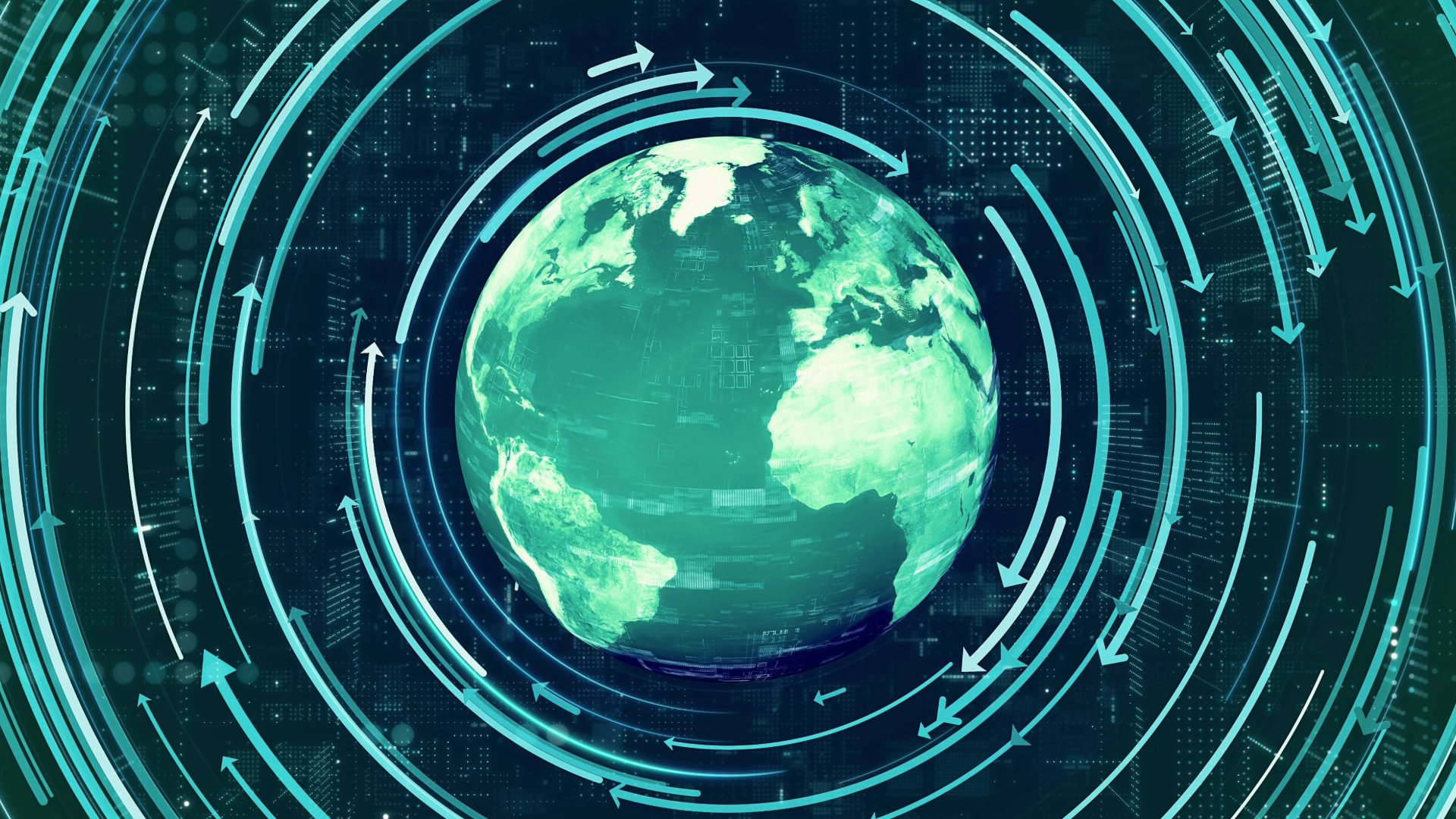
As part of our Thought Leaders series, Mewburn Ellis Associate Niles Beadman explores the microbial revolution and the promise it holds for the circular economy.
Forward: features discuss and celebrate the best of innovation and exploration from the scientific and entrepreneurial worlds.
Biomimicry has long been a stalwart of innovation. Nature has inspired a range of technologies, like the shape of bullet trains, based on a kingfisher’s beak, and LED pixels, taken from a butterfly’s wing. Biomimicry is now being taken to new heights as natural degradation processes are being supercharged to tackle modern day waste. Next generation food, packaging and fabrics are just some of the areas now inspired by nature.
Plastic eating microbes exist naturally, but are stifled by plastic’s tightly packed crystalline structure.
French company Carbios aim to overcome this by amorphising polyethylene terephthalate using heat, thereby opening the closed crystalline structure to enzymatic degradation. Key to this is modification of depolymerase enzymes to function at high temperatures. Natural thermophilic enzymes, thought to be the first life on earth, achieve thermal stability by reinforcing their polypeptide backbone. Analogously, Carbios append bulky, hydrogen-bondable sugars to the enzyme to achieve thermophilicity.
The University of Portsmouth, in partnership with the US Department of Energy, are also at the forefront of PET enzymatic depolymerisation. By studying the crystal structure of PET-depolymerases the group found that the enzyme’s active site was unusually open, hence its propensity to accept tightly packed man-made polymers. By computer modelling the enzyme-substrate complex, the team were able to adapt the active site’s conformation to boost the efficiency of the enzyme.
Unexpectedly, trees and plastics share some traits. Researchers at Yale recognised that lignocellulose polymers in wood are broadly isostructural with plastics, and screened endophytes inhabiting hardwood to see if any could decompose plastic too. From over 59 candidates, Pestalotiopsis microspore was identified to anaerobically depolymerise polyurethane as its sole food source.
Successful studies have also been conducted on landfill sites, in the hope that microbes might be thriving on the abundance of plastic.
However, degradation is only half the story. The ultimate form of biomimicry is where waste can be transformed back into useful materials – a circular economy. In nature, one organism’s trash is always another’s treasure.
Latest estimates found that animal derived proteins are responsible for at least 16.5 % of carbon dioxide emissions. Thus, research is focusing on alternatives for carbon intensive protein production.
A seminal example is mycoprotein, marketed as QuornTM, and grown from Fusarium venenatum fungus. The fungus has a meat-like texture due to its fibre length being similar to muscle. A newer player is Nature’s Fynd and their Fy ProteinTM. Fermented using fungus isolated from Yellowstone National Park, the fungus grows on a liquid-air interface to give a matted fibre network. Nature’s Fynd report the land and water usage is 99 % less than beef – and growth is so resilient it is said to be space ready.
Other approaches showing promise build on research into alternative protein-sources started by NASA in the 1960’s. Air Protein uses hydrogenotrophs to combine hydrogen and carbon dioxide to synthesise protein. The company’s recent international patent application explains that the protein is a specialist form of hydrolysate derived from chemoautotrophic microorganisms. Importantly, the inventors claim that the building blocks can be captured or generated anywhere, giving a flexible and scalable process.
Fabric production is another industry with significant environmental impact, for example accounting for 20% of global waste water.
Leather has proved a popular area for development due to its unique characteristics but high environmental cost. Ecovative Design have recently expanded into leather alternatives, leveraging their library of fungi to emulate cow hide, giving a natural appearance and tannable material.
Other brands such as ReishiTM, have worked on intertwining mycelium fibres to give a strong collagen-like structure. The process can also be fine-tuned to tailor strength, softness and drape, depending on the application.
The irony of selling innovative low-carbon products wrapped in plastic is not lost on the industry, and huge steps are being taken to revolutionise packaging too.
Ecovative Design have developed a range of myco-packaging materials, including foams (MycoFlexTM) and rigid bio-composites (MycoCompositeTM). This has been taken up by flat-pack giant IKEA, who announced plans to replace Styrofoam packaging with MycoComposite. Ecovative Design’s progressive technology was noted in the European Patent Office’s Patents for tomorrow’s plastics publication – which speaks to the rapid growth of patent activity in plastic alternatives.
Another contributor is UK company Shellworks, winner of Imperial University’s Venture Catalyst Challenge 2020, with their first generation product ‘Vivomer’. Feeding on carbon sources, the microbes build a fat-like storage system which has mechanical properties akin to plastic. The microbes originate from soil and marine environments, ensuring Vivomer is primed for decomposition in soil or sea – but can also be readily reused in a circular process.
Inspired by nature, this microbial revolution holds great promise for merging the circle of life with the circular economy across various industries.
Niles is a Patent Attorney working in the chemistry field. Niles has an MChem degree in chemistry from the University of Oxford. His undergraduate research project was on the synthesis of novel perylene diimide containing macrocycles for anion recognition and sensing applications.
Email: niles.beadman@mewburn.com
Our IP specialists work at all stage of the IP life cycle and provide strategic advice about patent, trade mark and registered designs, as well as any IP-related disputes and legal and commercial requirements.
Our peopleWe have an easily-accessible office in central London, as well as a number of regional offices throughout the UK and an office in Munich, Germany. We’d love to hear from you, so please get in touch.
Get in touch