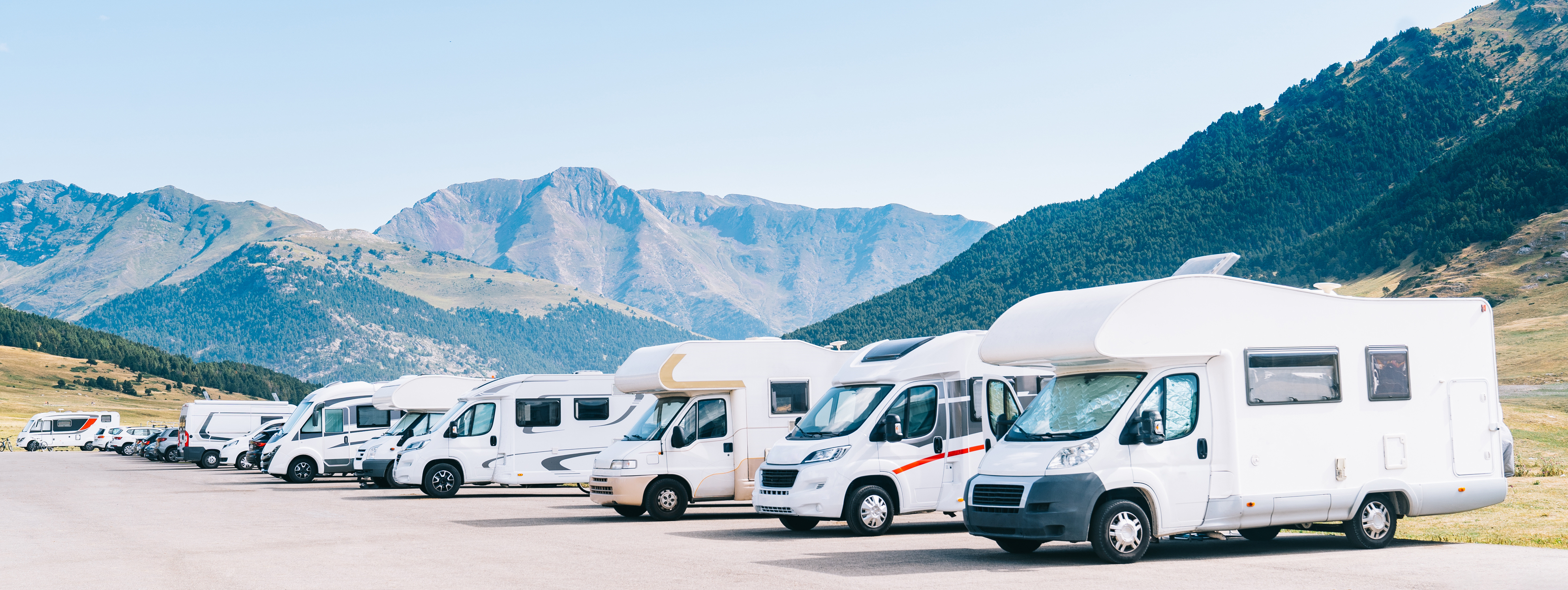
Printing with graphene is a large and growing field, representing a highly promising range of techniques for translating the unique properties of graphene (e.g. flexibility, electrical conductivity, sensing performance) into real-world applications. Development of graphene inks is therefore attracting interest both in academia and industry. The world’s first Graphene Hackathon is set to take place in November, encouraging teams to develop and demonstrate potential applications for graphene inks.
However, while printing offers many benefits, it is best suited to printing on flat surfaces such as sheets or reels of paper, plastic, or cardboard. Furthermore, many printing techniques are “contact” type processes, where the ink is transferred to the target surface by pressing it against a printing plate. Surfaces that are, for example, rigidly curved (e.g. plastic or glass objects), or compressible (e.g. foams, textiles) can be challenging or even impossible to print on.
Researchers from Dr Tawfique Hasan’s Hybrid Nanomaterials Engineering Group at Cambridge University, working in collaboration with interactive print media specialists Novalia Ltd have recently developed a new technique that allows this problem to be overcome. As reported in Dr Leonard Wei Tat Ng’s paper in Advanced Functional Materials, the process allows both individual graphene tracks (e.g. heating elements, strain sensors, touch sensors), as well as more complex functional devices (e.g. a capacitors) to be printed on such “non-printable” surfaces, including rigid curved surfaces such as glass and plastic, as well as deformable materials including latex (e.g. gloves), textiles (including medical dressings), and even food (in the form of gummy sweets and marshmallows). The technique therefore has the potential for applications in areas as diverse as low-cost sensing, internet of things (IOT) devices, and healthcare.
To achieve this, the device is first printed onto a sacrificial water-soluble polymer substrate using one or more water-insoluble inks. The printed device is then floated on water, allowing the substrate to dissolve while leaving the device intact. Finally, the device is fished from the water using the target object. The printed device conforms to the shape of the target object. Once the substrate and device have been dried (by placing in a low-humidity environment), the device is left adhered to the surface of the target object, with a level of adhesion comparable to that of commercially available conductive inks printed directly onto similar (flat) surfaces using conventional techniques. More importantly, the performance of the devices (as tested both before and after transferring to the target object) is not affected by the transfer process.
Lead author, Dr Leonard Wei Tat Ng says of the research, “our work, although now merely a demonstration, represents how we can combine legacy technologies with new materials like graphene to bring added value. Through a little bit of creativity, we can speed up the commercialisation of graphene and exploit its unique properties in never-before-imagined applications”.
This therefore represents a powerful demonstration of how the functionality introduced by printing graphene can be extended to these previously unprintable surfaces, with potential impacts across a wide range of sectors and industries.
This blog was originally written by Richard Howe.
Niles is a Patent Attorney working in the chemistry field. Niles has an MChem degree in chemistry from the University of Oxford. His undergraduate research project was on the synthesis of novel perylene diimide containing macrocycles for anion recognition and sensing applications.
Email: niles.beadman@mewburn.com
Our IP specialists work at all stage of the IP life cycle and provide strategic advice about patent, trade mark and registered designs, as well as any IP-related disputes and legal and commercial requirements.
Our peopleWe have an easily-accessible office in central London, as well as a number of regional offices throughout the UK and an office in Munich, Germany. We’d love to hear from you, so please get in touch.
Get in touch