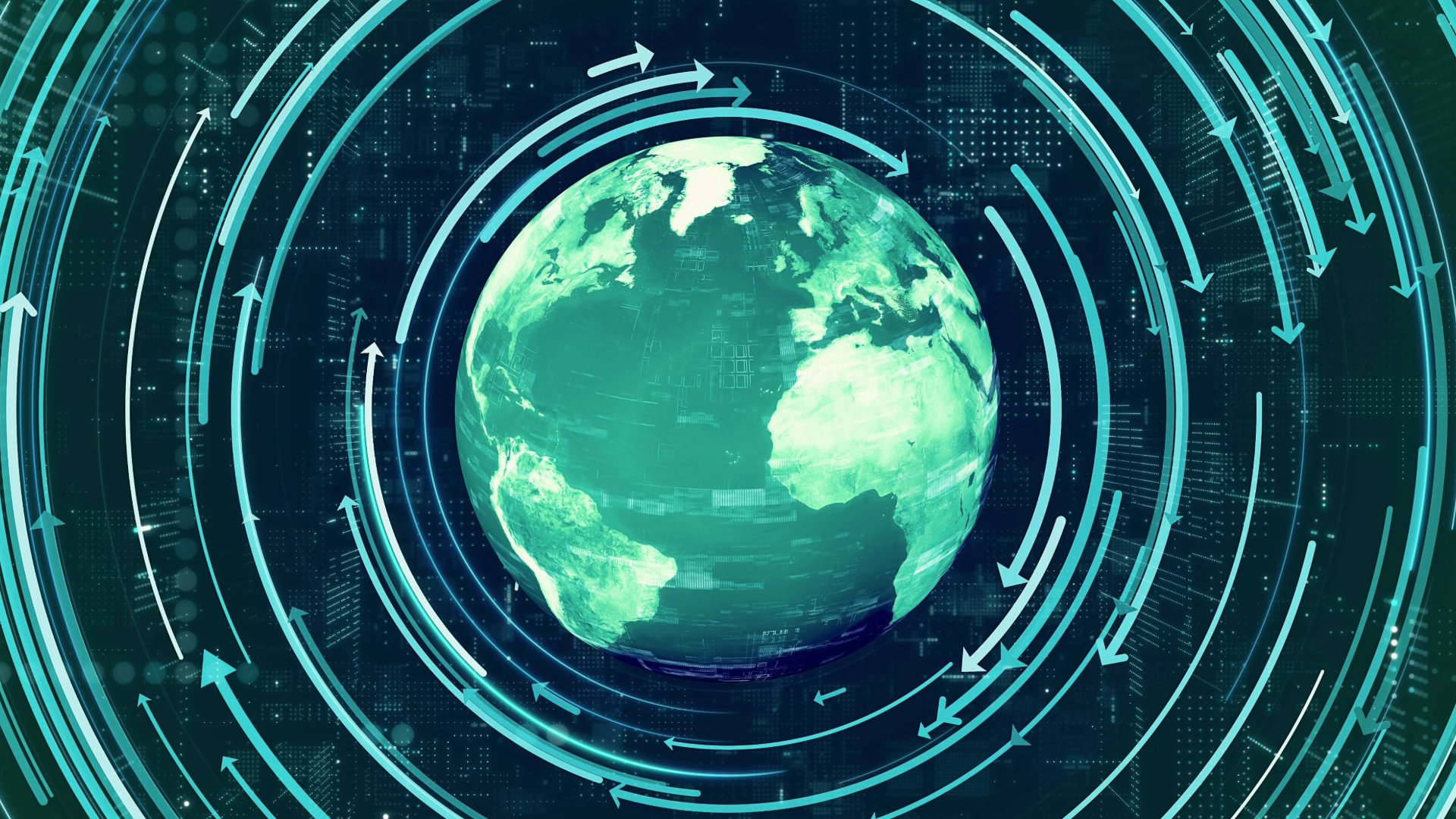
Efforts to improve recyclability are typically focused on high volume, bulk materials like plastic bottles or packaging. However, for composite products the minor components often provide a major barrier to recycling. For example, a paper coffee cup is made of 99% recyclable paper, but is barred from easy recycling by its integral polyethylene liner.
Similarly, despite printing and marking accounting for only the top few microns of a product’s surface, it can significantly influence recyclability.
Inks have historically been ignored during recycling. As the ink makes up a relatively small proportion of the product, it seems to have been accepted that the ink would be incorporated into the recycled material. However, ink contamination compromises the control and quality of recycled feedstocks and makes them less desirable for manufacturers, often resulting in so called down‑cycling.
I expect most people are familiar with the grey tinge of recycled plastic compared to virgin plastics – it is the cocktail of residual dyes and pigments that causes this (mis‑)colouration. As consumers we may be (now at least) more open to this ‘less appealing’ colour if a product is made from recycled material but there are many applications for which the residual colourants are fundamentally incompatible.
Perhaps due to increased scrutiny of the recyclability of products, innovations in ink recycling are happening all around the world. These innovations include new processes for recycling materials marked with well known inks all the way to developing new inks and printing processes that are inherently more sustainable from the outset.
Removing inks is costly and the organic solvents often relied upon could be seen to cause more harm than good. Now, new ‘cleaner’ ways of de-inking products promise to enhance their recycling potential.
Recent work by the University of Alicante and Austrian multinational EREMA focuses on a continuous water based process to strip ink from waste plastic. The University of Alicante’s international patent application explains that a basic solution having a pH of from 11 to 13 is used, with a combination of alkylammonium bromide and alkylsulfate surfactants.
The patent application also details a pigment recovery process, for extracting pigment from the washing solutions. This is said to enable re-use of the pigment - and more importantly the cleaning solution - lessening water and surfactant usage for large scale recycling.
Paper recycling faces similar challenges. Early paper recycling processes removed ink using a potent cocktail of peroxide and caustic soda to desorb the ink from the cellulose fibres. Biologically friendlier alternatives have since been developed, and modern paper mills rely on enzymes to digest inks. However, enzymes are notoriously picky about their working conditions, further increasing the cost of recycling processes. Laser prints, where toner is thermally fused to the paper, and hydrophilic ink deposits also prove difficult for enzymes to attack.
Nonetheless, recent work by Chonbuk National University in South Korea has found that low temperature plasma treatment may remove even the most stubborn inks, using only water.
As explained in their recent Nature article, helium plasma is used to treat the paper before the ink is removed by soaking in water. Their research shows that plasma treatment results in faster ink removal, which has the potential to reduce water usage and avoid the need for harmful additives. It is thought the highly pervasive plasma increases the hydrophilicity of the paper throughout its porous structure, increasing surface water contact thereby making washing more efficient.
Aside from ink removal, as with all other materials the ink itself also has a large part to play in enabling recycling.
While most commercial ink colourants find their origins in petrochemicals, biological colourants which are more sustainable to produce and remove are now emerging. One burgeoning example is from US company Living Ink, who use extracts from algae as the main colourant in their “Algae Ink”. This carbon negative pigment has recently been taken up by major brands such as Patagonia for use in their packaging.
However, the colourant is only a minor component of most ink compositions. Innovation in the liquid carrier, the major component of many inks, is also key to improving recyclability.
Cambridge-based Domino Printing Sciences have recently developed a new line of vegetable oil based inks, replacing conventional mineral-oil carriers. Domino say this ink is particularly suited for use on cardboard products, and is designed to boost cardboard’s recyclability. Another focus for Domino is on more frugal inkjet printer technologies, with their latest piezo inkjet printer achieving a one third reduction in ink usage - further minimising the environmental impact of the printing process and end products.
Ink application and removal, as well as the ink itself, play a key role in lowering the barriers to product recyclability and increasing the quality of recycled feedstocks. It is encouraging to see innovation at all stages of the ink lifecycle appearing across the industry, and it will be interesting to see how this impacts the shift towards a more circular economy in the future.
Niles is a Patent Attorney working in the chemistry field. Niles has an MChem degree in chemistry from the University of Oxford. His undergraduate research project was on the synthesis of novel perylene diimide containing macrocycles for anion recognition and sensing applications.
Email: niles.beadman@mewburn.com
Our IP specialists work at all stage of the IP life cycle and provide strategic advice about patent, trade mark and registered designs, as well as any IP-related disputes and legal and commercial requirements.
Our peopleWe have an easily-accessible office in central London, as well as a number of regional offices throughout the UK and an office in Munich, Germany. We’d love to hear from you, so please get in touch.
Get in touch