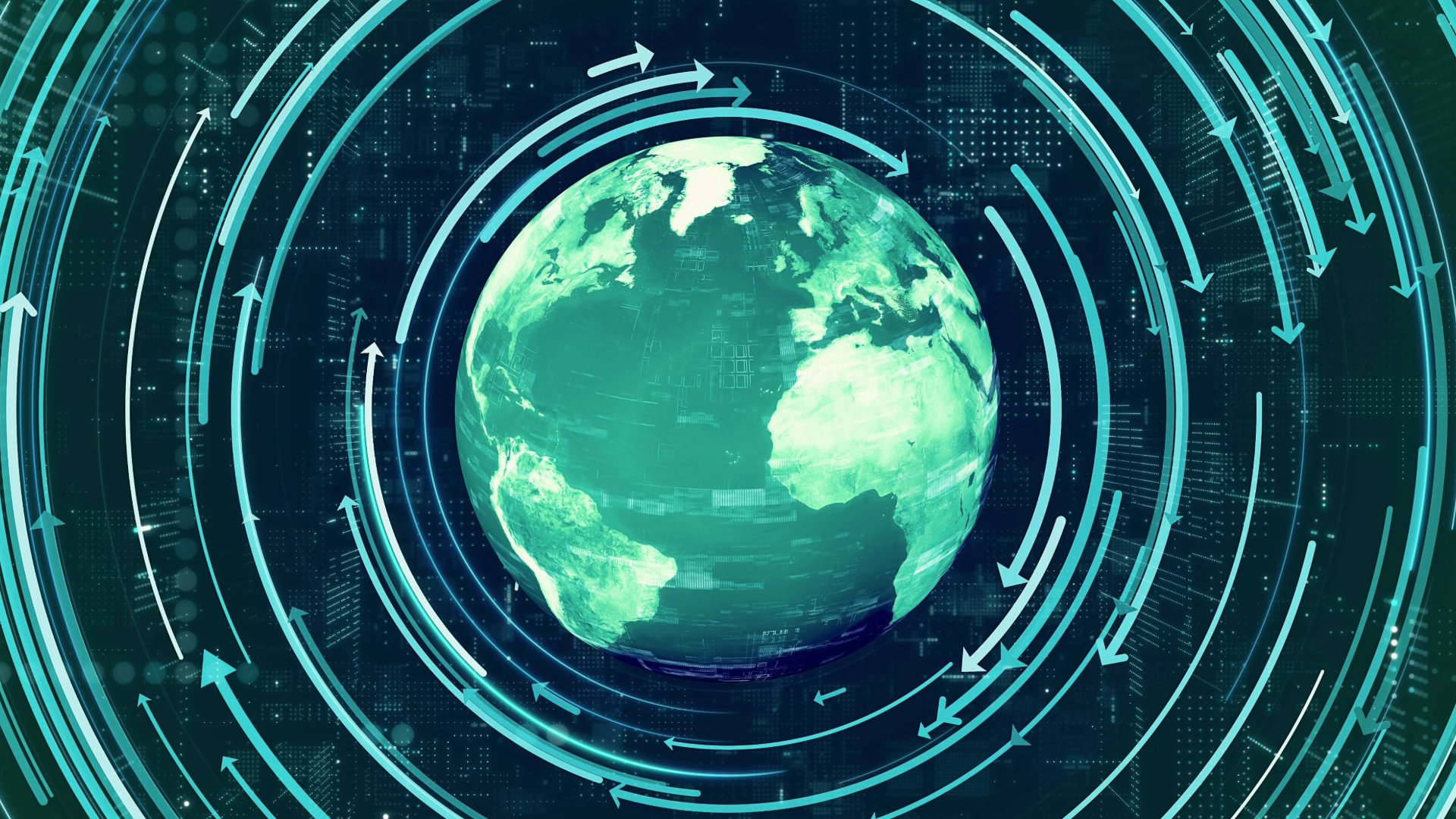
Single-use plastic has become indispensable in everyday life, particularly in the packaging of household goods – it is estimated that in the UK we throw away a staggering 1.85 billion pieces of plastic packaging each week! This accounts for nearly 70% of the UK’s plastic waste.
Since the early 2000s, the UK population has been urged to recycle their plastic waste, yet The Big Plastic Count 2022 revealed only 12% of our plastic packaging gets recycled. One of the reasons for this is that our recycling infrastructure struggles to cope with the vast amount of plastic, and this is exacerbated by the abundance of coloured plastic. Despite being incredibly useful by providing visual appeal, distinguishing brands, and helping to categorise related products, coloured plastic contaminates recycling streams, thus causing problems with the sorting process, and is often not recycled at all.
Standard plastic recycling systems typically include a range of sorting mechanisms including magnets and eddy currents to remove metals, mesh sieves to remove dust and dirt, and a plastic sorting system to sort the plastic waste by polymer type and colour. The stream of plastic waste is initially sorted using near-infrared (NIR) sensors which identify polymer type by measuring each polymer’s unique absorption spectrum at NIR wavelengths. Once sorted into polymer types, the stream is sorted using optical sensors to separate the plastic by colour: clear and white plastic can be recycled back into clear and white plastic, whereas coloured plastic is typically recycled into much less versatile grey-ish or black plastics, or it may be simply sent to a landfill.
Straight-forward solutions to such problems with coloured plastic include companies simply switching to clear or white plastic which is more recyclable (for example, Co-op recently cleared their shelves of coloured milk bottle tops), or using alternatives to plastic such as paper-based packaging which generally has a less significant negative impact on the recycling process. Ultimately though, maximising accuracy and efficiency in the sorting process is essential to make the plastic economy circular and sustainable.
The presence of coloured pigments in plastic recycling streams makes it harder to obtain recycled plastic with vibrant and distinct colours, and the resulting product is usually restricted to being used for grey or black products. This contributes to the demand for virgin, often oil-derived, plastic which can be coloured exactly as desired. Methods of removing coloured inks from the surfaces of plastics to improve recyclability have been developed (something we have discussed in a previous blog about innovations in ink recycling), but these processes do not remove the colour from the plastic itself. Hence, many companies are working hard to mitigate the impact of pigmented plastic on the circular economy.
For example, white plastics are often incorrectly sorted into the clear plastic stream because the optical detectors struggle to differentiate them. The presence of white plastic makes the recyclate murkier, significantly devaluing the otherwise highly versatile clear plastic end-product. Unfortunately, white pigments are essential components in the plastic packaging of certain products, such as UHT milk where an opaque light barrier is required to prevent photo-degradation, and so their elimination is not straightforward.
Titanium dioxide is the dominant white pigment used in plastics, and global chemistry company Chemours is leading the way to mitigate its effect on the recycling process. By co-ordinating the Remove2Reclaim initiative, and with the help of collaborators Catalisti, INEOS and a handful of others, they have created a sorting mechanism to identify plastic containing TiO2, and solvent-based extraction systems which recover the pigment. They hope that this innovation will allow both pigment and polymer to be separately recycled. Consequently, white plastic can remain part of the circular plastic economy.
Other players in the industry are developing innovative ways to separate all pigments into a waste stream to provide a de-pigmented plastic stream. Impact Laboratories Ltd., in their granted patent GB2570019B, describe a process which achieves this without the long processing times, high energy requirements and carcinogenic solvents of existing methods. The patent describes an example of the process that makes use of ionic solvents and a high shear mixing mechanism to create maximum interaction between the solvent and the pigment – and the solvent is immediately recycled back into the incoming feedstock. Ionic liquids are reportedly excellent for the job as they can be reused up to 25 times before their efficacy is degraded, they can be tailored to solvate specific organic and inorganic small molecules, they often will not evaporate under high temperature use, and they can be made from non-toxic, environmentally sustainable materials.
Black plastic has long been a particularly notable adversary of recycling efforts. Carbon black is by far the most popular black pigment due to its high colour strength and low cost. Unfortunately, it also happens to absorb across the NIR spectrum, which means it is impossible to identify the polymer’s characteristic peaks because no NIR wavelengths are reflected back to the detector. Hence, plastics containing carbon black are usually discarded and not recycled.
One way to tackle this problem is to switch from the vastly abundant carbon black pigment to an NIR-detectable black pigment. Consumer goods giant Unilever, a founding member of The UK Plastics Pact, has done just this in their iconic TRESemmé® and Lynx® packaging. Thankfully, there are many companies developing such pigments – for example, Heubach has 3 different detectable black pigments on the market, each one suitable for a different plastic type, and these are compatible with existing recycling technology. Lanxess has had its manganese ferrite black pigment Bayferrox® 303T on the market for decades but its potential as an NIR-detectable pigment has only become apparent in recent years. More recently, BASF’s 2022 PCT publication describes complex, multi-ring organic molecule NIR-transparent black pigments which can be used in recyclable plastic products, as well as having uses in the aerospace industry due to its lower thermal absorption.
Other companies are taking a different approach, and devising alternative ways to handle recycling of carbon black so that it need not disappear entirely from plastic products. For example, Unilever has identified that some detectable black pigments are less colour-effective in recycled articles than in those made from virgin plastic. Hence, they have proposed a solution in the way the packaging is constructed which allows traditional black pigments to still be used. A multi-layer system where the black plastic is covered by a layer of clear plastic (of the same polymer) can be detected because the outer layer is detectable. This is described in, for example, their granted European patent EP4096928B1, where packaging has an NIR-detectable outer layer and an NIR-undetectable inner layer, both being made of at least 95% recycled plastic.
Tackling the issue in a different way, circular economy innovators SMX are striving to make the world of commerce more transparent and more sustainable. The company has recently filed a range of patent applications directed to x-ray fluorescence (XRF) markers which can be added to materials in specific ratios to provide an invisible signature which can label objects with information about their make-up, date of origin and place of origin, amongst other things. In their PCT application WO 2022/118320 A1, they specifically explain how this technology can be applied to black plastic, allowing it to be detected and its polymer type labelled so that it can be correctly recycled. The markers can also be used to show how much of a plastic object is made from virgin plastic compared to previously recycled plastic. Only a very small amount of the XRF-detectable composition needs to be contained in the plastic relative to the amount of carbon black, and the XRF signature can even be read below the surface level, for example if covered by a film or dirt. It’s not yet clear to what extent this technology is compatible with existing recycling systems, or whether different and/or additional installations will be required.
Another approach being made possible by Canon is to adopt new sensors in recycling plants which use Raman spectroscopy instead of NIR. Raman spectroscopy is a slower technique, which previously hasn’t been quick enough to analyse plastic on the passing conveyor. Canon has just unveiled a new system which is able to track individual plastic fragments as they move along the conveyor, thus providing enough time to obtain their Raman spectrum and sort by polymer type, whether carbon black is present or not! This system uses a proprietary receiving system, Raman spectrometer and recognition software. Although this requires adaptation of the current infrastructure, no modifications to the packaging itself is needed. The Japanese optics giant hopes to deploy this technology in the first half of 2024.
Plastic is such an inherent part of our lives that it’s unlikely to go away any time soon. As a society we are continually coming up with ways to reduce the negative impact of plastic; for example, we’ve recently written about self-degrading polymers and plant-based alternatives.
With existing plastic materials, we can use innovation to make the plastic circular economy bigger and stronger than ever by broadening the types of plastic products we can recycle. Coloured plastic remains a real problem, but there are more and more clever techniques and materials being developed each year to overcome this issue.
Matt is a trainee patent attorney in our chemistry team. Matt has a BSc and MChem in Chemistry and Mathematics (Joint Honours) from the University of Leeds. His Master’s research project involved the synthesis and characterisation of metal-organic frameworks incorporated into polymer films which have potential for use in hydrogen fuel cells. Matt also carried out a summer research project funded by the Royal Society of Chemistry which utilised computational chemistry to model reactions in the interstellar medium.
Email: matthew.barton@mewburn.com
Our IP specialists work at all stage of the IP life cycle and provide strategic advice about patent, trade mark and registered designs, as well as any IP-related disputes and legal and commercial requirements.
Our peopleWe have an easily-accessible office in central London, as well as a number of regional offices throughout the UK and an office in Munich, Germany. We’d love to hear from you, so please get in touch.
Get in touch